FAQ
1. How to guarantee the steel quality of steel billet? JST has its own steel mill. The product gives priority to excellent special steel continuous casting pipe billet. It owns the annual output of 1.3 million tons of pig iron, 15.01 million tons of steel, 700,000 tons of pipe billets, 600,000 tons of bars, 2 million tons of high-quality thread steel, 1 million tons of high-speed wire rods and 2 million tons of medium plates. Steel plant has advanced pipe billet production technology, which makes it able to control the steel quality of steel pipes and absolutely guarantee pure steel tube billets.
2. How to ensure the straightness of steel? JST configures two sets of international advanced Siemens electronic six roll straightening machines. In strict accordance with the standards or customer requirements, we can ensure the straightness of steel pipes after the heat treatment.
3. How to make steel tube achieve stable performance? JST has a number of testing equipment configured with micro-oxidation and non-oxidation heat treatment furnace that can ensure there is no oxide layer on the surface of pipe and thus extends the service life of steel pipes. Our company also has a variety of flaw testing equipment or flaw detection machines, such as eddy current, magnetic flux leakage testing, ultrasonic testing, UNICORN ultrasonic joint detection machine, magnetic particle inspection machine, hydrostatic machine, etc. They are used to do horizontal, vertical and diagonal defect inspections for steel tube body, pipe ends and coupling. In addition, for obvious defects on the steel surface, JST also employs specialized technical personnel for manual monitoring. These technicians are trained and obtain the relevant qualifications before formally carrying out inspection work. They can deal with possible defects on the inner and outer surfaces of steel pipes and make appropriate treatments to ensure roundness and uniform wall thickness. JST has a professional research and development center and physical and chemical testing center. All of these equipment and personnel ensure stable performance of steel tubes.
4. What is the outer packaging of tubes?- There are two basic packaging methods for steel pipes. One is the ordinary bundling type and the other is similar with container loads. Bundle packaging would avoid the damage to pipes during bundling and transportation. The bundling labels should be uniform and consistent. The same bundle of steel tubes uses the same heat number (batch), steel grade and same specification. This will not cause mixed furnace (batch) bundling. The ones with less than a bundle can be packaged as a small bundle.
- When bundling the flat steel pipes, the end should be aligned. The difference of aligned tube ends should be less than 20 mm and the length difference of each bundle is less than 10 mm. But for the steel tubes orders according to the usual length, the length difference of each bundle is less than 5 mm. The length of the longest tube and the second longest tube should not exceed 10 mm.
-
For the steel pipes that are equal to or longer than 6 m, we should use at least 8 belts for each bundle, with three groups like “3-2-3”. For the steel tubes with the length of less than 6 m, we should use at least 5 belts for each bundle, with three groups like “2-1-2” (Two belts in the two ends and one in the middle). For the steel pipes that are equal to or longer than 3 m, we should use at least 3 belts for each bundle, with three groups like “1-1-1”. If there are some special requirements, you can add 4 plastic snap rings or nylon ropes on the single pipe. Fasten snap rings or loops firmly and steel tubes will not be loose and fall off during transport.
- The compartment should be clean inside. We should make sure that there is no stone, brick and other hard objects to prevent steel tubes from damage.
- For bulk or bundled steel pipes, we put sleepers in the bottom of compartment. For the flat-bed vehicles adopting steel bracket, we must install protective rubber mats on the side in contact with steel tubes.
- We should put at least two isolation sleepers or crossties vertical to pipes when they are sent to the warehouse.
- For long-distance transportation of finished steel pipes delivered to the user, we should tie them up tightly. If we use steel wires or similar hard objects for binding, the protective spacer is often placed in the steel strapping place to prevent damage to the pipe surface, to avoid pipe direct collision and friction with the compartment.
- Steel tubes to be delivered are shipped in strict accordance with furnace number (batch).
- There are various materials to produce seamless tubes in the market. The most common 10# and 20# low-carbon pipes are mainly used in fluid-conveying pipes. Seamless tubes made of 45 and 40Cr carbon steel are used for manufacturing machinery force components. Hot-rolled steel pipes are delivered in hot-rolled state or heat treatment state. Cold-rolled steel tubes are delivered in heat treatment state. General seamless pipes are done with strength and flattening tests before leaving factory.
- The rolled steel plates are usually with the continuous casting billet thickness of 230 mm. After coarse rolling and precision rolling, the final thickness is between one to twenty millimeters. Because the width thickness of steel plate is small and the dimensional accuracy requirements are relatively low, it is not easy to deform. Seamless steel tubes can control the micro structure and mechanical properties by controlling the start rolling temperature, final rolling temperature and curling temperature.
- High pressure boiler pipes are used below 450℃. Mostly national pipes are hot-rolled or cold-drawn steel pipes manufactured from 10# and 20# carbon steel. Because they stay in high temperature and high pressure conditions for a long time, influenced by high temperature smoke and steam, they will be oxidized and corroded. Therefore, steel tubes are requested to have high strength, high resistance to oxidation corrosion and have good organizational stability. They are mainly used to manufacture water-wall tubes, boiling water pipe, superheated steam pipe, superheated steam locomotive boiler tubes, big and small smoke pipe and arch brick pipe, high pressure and high pressure boiler superheater tube, reheater tube, main steam pipe, etc.
- Structure seamless pipe is mainly used for general structure and mechanical structure.
- Fluid seamless steel tube is applied in major projects and large-scale equipment for the delivering fluid.
- Seamless steel pipe for low and medium pressure boiler is mainly used in industrial boilers and life boiler pipelines to transport low pressure fluid.
- High pressure boiler seamless steel tube is mainly used in power plant and nuclear power plant boiler tanks and pipes that are resistant to high temperature and high pressure.
- Marine seamless steel pipe is mainly used in ship boiler and superheater I and II grade pressure tubes.
- Seamless pipe for high pressure chemical fertilizer equipment is mainly used in fertilizer equipment for the transmission of high temperature and high pressure fluid.
- Petroleum cracking seamless steel tube is mainly used in boiler, heat exchanger pipes in petroleum refinery for conveying fluid.
- Cylinder seamless steel pipe is mainly used for the production of gas and hydraulic cylinders.
- Hot-rolled seamless tubes for hydraulic prop is mainly for the production of coal mine hydraulic props and cylinders.
- Cold drawn or cold rolled precision seamless steel tubes are mainly used for mechanical structure and carbon pressure equipment They are required with high dimensional accuracy and high surface finish.
- Seamless steel pipe for hydraulic and pneumatic cylinder with precision internal diameter is a kind of cold drawn or cold-rolled seamless steel tube. It is mainly used for production of hydraulic and pneumatic cylinders with precision diameter.
- Structural stainless steel seamless tubes are mainly used for general structures (hotel and restaurant decorations) and chemical company mechanical structure that is resistant to atmosphere and acid corrosion and has certain strength.
- Seamless pipe for automobile axle service is mainly utilized for the production of automobile axle casings and high-quality carbon structural steel and alloy steel hot-rolled seamless steel pipes.
- Hot Rolling
- a. Advantages
Hot rolling can destroy the ingot casting organization, refines steel grain and eliminates defects in the microstructure, so that the structure and mechanical properties of steel pipe are improved. The pouring bubbles, cracks and porosity can be welded under high temperature and pressure. - b. Disadvantages
After hot rolling, the non-metallic inclusions (sulfides, oxides and silicates) within the steel are pressed into sheets and delamination (interlayer) phenomenon occurs. Delamination makes the steel tension performance deteriorate significantly, and interlayer tear may occur during the weld shrinkage. Residual stress is caused by uneven cooling. Generally the larger cross-sectional size, the greater the residual stress is. It may produce adverse effects on deformation, stability, antifatigue, etc. - Cold Rolling
- It means that in normal temperature, we can make steel plates into various steel products through cold drawing and clod bending.
- a. Advantages
It features fast forming speed, high yield and does not damage the coating. We can make a variety of cross-sectional forms in order to adapt to the use conditions. Cold rolling can also make steel tubes produce large plastic deformation, thereby increase the yield point of steel. - b. Disadvantages
Although the molding process has not experienced hot plastic compression, but there are still residual stresses within the cross-section that will influence the overall and local buckling characteristics of steel. Cold-rolled steel style is generally with open section, making low free torsional stiffness of steel. It is prone to bending and torsional buckling. The torsional performance is poor. Cold formed steel pipes are with small wall thickness and so they have poor capacity to withstand localized concentrated load capacity. - The main differences of hot-rolling and cold rolling
- a. Cold rolled steel sections allow local buckling, which can make full use of the capacity after rod buckling while the hot-rolled steel tubes do not allow local buckling occurring.
- b. The residual stress of hot-rolled and cold-rolled steel pipes are produced differently, so the distribution on the cross section are quite different. For cold-rolled steel sections, the residual stress distribution is curved, but for hot rolled or welded steel tubes, residual stress distribution on the cross-section is a thin film type.
- c. The free torsional stiffness of hot-rolled steel is higher than that of cold-rolled steel. Thus the torsional performance of hot-rolled steel pipe is better than that of cold-rolled steel tubes.
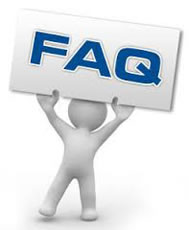
- Home
- About Us
- - Group Overview
- - Company Profile
- - Brand Development Path
- - FAQ
- - R&D Strength
- - Project Achievements
- - Why choose us
- - Download
- News
- Products
- API 5L Line Pipe
- - Onshore Line pipe
- - Offshore Line pipe
- - Through Flowline(TFL)
- - PSL-2 Line Pipe Applied in Marine
- - Acid Corrosion Resistant PSL-2 Line Pipe
- - PSL-2 Sour Service Line Pipe
- - DNV ABS LR API Line Pipe
- - X52 X60 X70 X80 QS Line Pipe
- - Coating of Line Pipe
- API 5CT
- - API 5CT Series Coupling
- - API 5CT Series Tubing
- - API 5CT Series Casing
- - API 5CT Coupling Stock
- - API 5CT Pup Joint
- JST Special Series of Tubing and Casing
- - Perforating Gun Pipe
- - Collapse Resistant Casing
- - Ultra High-Strength Casing
- - 3Cr Corrosion Resistant Tubing & Casing
- - Anti-H2S Corrosion Tubing
- - CO2 Corrosion Resistant Tubing
- - Low Temperature Service Tubing and Casing
- - Heavy Oil Thermal Pipe
- - Premium Connection
- API 5DP Drill Pipe
- Anticorrosion Steel Pipe
- International Standard
- - ASTM/ASME Standard
- - EN Standard
- - DIN Standard
- - JIS Standard
- Steel Tube Applications
- Steel Tube Process
- Quality
- - Certificates
- - Production Process
- - Online Test
- - Physical and Chemical Test
- - Quality Assurance
- - Technical Services
- - After Service
- - Cost Savings
- Views
- - Cooperation and Communication
- - Steel-Making Mill
- - Tube-Making Mill
- - Tube Processing Mill
- - Heat Treatment Mill
- - Online Test
- - Physical and Chemical Test
- - Key Equipment
- - Products Details
- - Higher Steel Grade Product
- - Packaging and Transportation
- - Warehouse & Inventory
- Environment
- - Training
- - Work in JST
- Careers
- Contact Us